Volume 2 - Year 2014 - Pages 13-22
DOI: 10.11159/ijmem.2014.002
Interdisciplinary Semantic Interactions within a Unified Feature Model for Product Cost Estimation
Narges Sajadfar¹, Luis Campos Triana², Yongsheng Ma³*
¹University of Alberta Edmonton, Alberta T6G 2G8, Canada
sajadfar@ualberta.ca
²McCoy Drilling & Completions Farr Edmonton, AB, Canada
lcampos@mccoyglobal.com
³4-9 Department of Mechanical Engineering, University of Alberta,
Edmonton, Alberta T6G 2G8, Canada
yongsheng.ma@ualberta.ca
Abstract - This paper reports a preliminary investigation on automatic cost estimation with a feature-based semantic model. Cost feature has been defined by the authors as a unique class in the unified feature modelling system to address the characteristics of cost engineering entities, constraints and dependency relations. This paper describes the relations between a cost feature and three engineering sub-models, i.e. machining model, design model and other auxiliary data model by associating tangible and intangible data. Further, semantic relations are investigated in early product design process for dynamic, accurate and visible product cost estimation. This paper also discusses cost engineering related functions, associated data structures, and techniques proposed in details. A case study is used to show cost feature properties and functions. Also they are used to illustrate the interactions with the three engineering sub-models to verify the relations.
Keywords: Cost estimation, semantic modelling, cost feature, design feature, machining feature, unified feature modelling.
© Copyright 2014 Authors - This is an Open Access article published under the Creative Commons Attribution License terms. Unrestricted use, distribution, and reproduction in any medium are permitted, provided the original work is properly cited.
Date Received: 2013-11-13
Date Accepted: 2014-03-28
Date Published: 2014-04-09
1. Introduction
Historically, attaining accurate cost estimation is a critical factor in business success, because cost engineering has a great effect on the manufacture profitability and management. Timely and accurate cost information helps business to make good decision and reduces business risks. Also, accurate cost estimation can create a competitive advantage. A good cost estimation method has a direct effect on sale price, amount of sales, market share, and enterprise profits [1]. The cost management function can be developed within the common Enterprise Resource Planning (ERP) systems. Those successful companies that can offer the best price within the short time on market will increase their market share. Lots of techniques and methods are introduced by researchers for product cost estimation in recent decades. There have been number of researches about cost estimation modelling and most of them focused on parametric and historical data [2]. Feature-based cost estimation is an analytical cost estimation technique which is more focused on quantitative approach rather than qualitative approach [1]. The main goal of feature-based cost estimation is to calculate the product total cost based on identified cost-related features. The most quoted limitation of feature-based cost modelling is the difficulty to maintain the semantics cost related of features during the product lifecycle. To avoid this limitation, the complex cost-related features, and the relations among other types of features have to be managed consistently.
As reported in authors' recent paper [3], a new feature-based semantic model was conceptually proposed. This model proposes a data mining algorithm to identify tangible and intangible data that is related to cost. Then related design features and machining features need to be identified. Cost feature has been defined [4] as a unique category of features in a unified feature scheme [3] that can cover all types of features which are related to cost estimation. As a result of associative feature modelling [5] which could support the cost feature concept, then using just one kind of features generically so that it can be well defined class to be semantically maintained during the product life cycle is a feasible and effective approach. In such a way, the properties and behaviours of other extended features defined on top of the generic feature model will be updated automatically. Figure 1 shows three sub-models, i.e. design model, machining model, and all other auxiliary data including tangible data, which refers to the set of data that has been computerized and can be extracted automatically by certain program interfaces, and intangible data which requires user's input interactively on spot based on human experience and knowledge. These three sub-models have conceptual semantic relations with each other's. The purpose of this paper is describing a new cost estimation functional module and its semantic interactions within the aforementioned three sub-models and illustrating the effective definition and use of the cost feature objects which can be directly usable in computer functions for the cost estimation at different engineering phases or levels, such as the design and manufacture stages.
2. Design Model
Refer to Figure 1, in this research, the suggested design model is feature-based that includes four sub-models: material requirement, functional assembly feature, functional part feature and part geometry construction feature. The design model is created in the first phase of a product life cycle and enhanced or modified throughout other downstream stages including manufacture stage. It can be appreciated that the design model has a significant role in cost estimation. Design model is detailed gradually based on the model's analyses by the way of further defining the model functions and purposes of the product. It should consider processes of product's manufacture. Generally, each design cycle has three main stages: conceptual design, preliminary design and detail design [6]. Conceptual design is about definition of product functions, requirements, ability and possible solutions. During preliminary design a few solutions will be select for more analysis. Finally, the best solution will be selected at detail design stage with more detail.
There are several ways for describing well-defined design model, such as design for manufacturing, assembly, lifecycle, recycling, cost and etc. [7]. Design model also needs to include manufacturing methods, i.e. design for manufacturing (DFM) sub-module. It is a systematic approach that considering available facilities, tools and capacity in purpose of design product with features that can be simply and economically manufactured. DFM is the combined practice for designing component functions and strengths with additional considering elements according to the manufacturing requirements. DFM describes operations such as welding, cutting and milling for each component. For example, for a welding operation, it needs to describe the position, height, length and weight of welding and all the profiling information. In this way, the design model is more based on machine model to increase the accuracy and manufacturing flexibility. However, in the design model, it does not have enough input to include real-time machining information such as the feed rate. The designing for cost is a common demand in the purpose of reducing product cost, but so far many companies have difficulty to organize and extract the useful data for this advanced application aspect.
The contents of design features can be changed during design process and the development of sub-models, therefore, well-defined design features need to be used [3] to keep the consistency. The designer can use the feature-based technique with a persistent design feature during design process. However, it is necessary to distinguish that design features are not interchangeable with manufacturing features [8]. Figure 2 illustrates the model and two views of a key component in an oil drilling equipment manufacturer, referred to as door weldment as a real case study. Table 1 shows the member work piece information of the door weldment. In CAD model, each member work piece in drawing can be defined as a design feature. For example during conceptual design door spacer is defined as a side impact protection feature. During the detail design, then the exact location, size and material of the feature are defined; and then some material cost related data can be worked out.
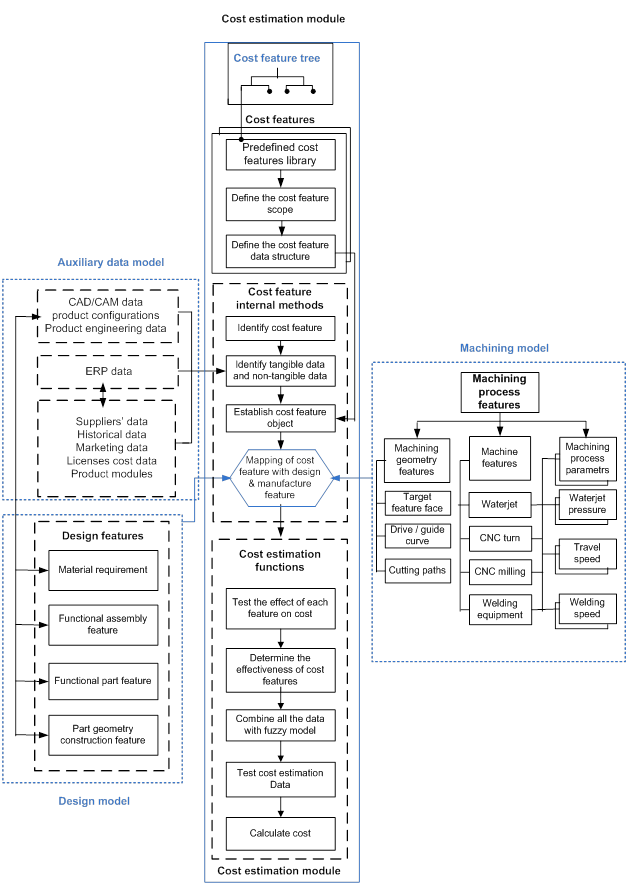
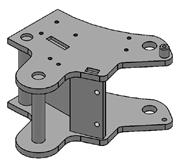
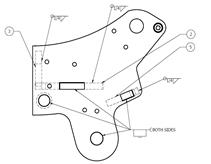
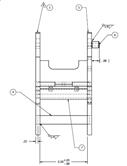
Table 1. Detail design information for work pieces before welding.
Item |
Qty |
Work piece name |
Purpose |
Standard |
Material code |
1 |
2 |
Plate |
Door RH |
U.S |
50860 |
2 |
1 |
Plate |
Door Spacer |
U.S |
50860 |
3 |
1 |
Plate |
Door Spacer |
U.S |
50860 |
4 |
1 |
Post |
Door |
U.S |
51920 |
5 |
1 |
Plate |
Door Spacer |
U.S |
50860 |
6 |
1 |
LUG |
Door Cylinder |
U.S |
50741 |
7 |
1 |
Post |
Door |
U.S |
51920 |
3. Machining Model
The suggested machining model in this paper is also feature-based. Each manufacturing process is modelled as a machining feature which can be initiated from predefined templates and fully generated with extracted feature entity information. A machining feature associates the blank geometry, the related target part geometry, cutting geometry; machines used, and detailed process conditions. This machining model has to represent the involved machining data and entities via features; also, it has to manage the relationship among the entities and the process data.
Figure 1 provides some breakdown of the machining model, which has two main parts: machining features and machining process. A machining feature's geometrical entities are generally defined as a set of faces and tool path driving curves defined by referring to the part geometry derivatives; the part and the derivatives are represented with the Boundary Representations (B-Rep) solid model format. Feature geometries are defined according to the traditional features associated with specific machining processes, such as holes, slots, pockets, that need to be identified from the model of the final product [8]. There are several approaches for machine feature reorganization such as graph-based, volumetric decomposition and hint-based [8]. Many researchers also have attempted to define a standard set of machining feature, such as the Standard for the Exchange of Product Model Data (STEP) that has been an international standard for representing engineering data structure and exchanging product data model [3]. Theoretically, with the generic feature concept and further research work, other user defined machining features can be incorporated as well. However, cost information data structure associated to design and manufacture feature are not well defined. Table 2 shows the cost elements related to some manufacture processes for a door weldment. Five different operations are needed and the machining features costs should be linked with associated defined elements.
In addition, the machine configuration information such as equipment type, power, dimensions, allowed interpolation, access and traversing directions, rotating, and positioning attributes of each machine are modelled in the form of machine features. Machine cost has to be considered as well.
Table 2. Manufacture Information.
Operation sequence |
Operation Code |
Operation Description |
Run |
Run Type |
Setup Cost per hr |
Run Machine per hr |
1 |
Water jet |
Cutting |
1.3 |
HRP/PC |
$30 |
$60 |
2 |
Man-Saw |
Cutting |
6 |
MIN/PC |
$30 |
$60 |
3 |
Drill & Tap |
Drilling |
4 |
MIN/PC |
$20 |
$50 |
4 |
Man-Lathe |
Turn/Face |
9 |
MIN/PC |
$30 |
$60 |
5 |
Weld |
Welding |
3.2 |
HRS/PC |
$10 |
$25 |
6 |
Mill |
Milling |
0 |
HRS/PC |
$30 |
$60 |
4. Auxiliary Data Model
Auxiliary data model is a collection of "design for x" data model under the concurrent engineering concept, which supports product development and manufacturing with certain specific engineering and optimization aspects. This model can be recognized as a data association system that enables the sharing and updating mechanisms of system integration across the product life cycle stages. For example, lots of tangible data need to be associated for product cost estimation such as CAD/CAM data, product configurations, profiling information, ERP data, available machines, supplier's process and cost data, and product quality models. All of these data sources and uses need to be identified at first step of auxiliary data model. Product feature library can define the commonly used classes or objects information as templates to gather cumulative enterprise knowledge and all the associated information more accurately.
To introduce the proposed cost engineering feature model, a cost feature definition is hereby given: Cost feature is a class type under object-oriented software engineering methodology, representing an abstracted types of costing items in the form of commonly recognized patterns, which contains the characteristic properties and behaviour functions. The properties include characteristic attributes, geometrical entities (including sub-features), referenced entities (including other features), etc. The supporting methods of the class include creating, managing and deleting predefined relations among the member entities, evaluation and validation methods of the attributes and entities of the class; and the expected behaviour functions according to the generic needs of cost engineering applications. Then individual cost features as objects can be instantiated from the cost feature class to materialize individual applicable cost items.
Given the variety of cost items to be considered in engineering, cost features can have different variations and they can be accommodated by applying object polymorphism techniques. So are the cost feature member entities and attributes. The main idea in this research is that cost feature member attributes and entities can be identified and modelled with the help of data mining (DM) technique. The start the description, the scope of cost feature data mining approach must be defined. It should be started with the scope of data mining.
As we have discussed before, there are many sources of tangible data for cost engineering. For example for an existing common part, we can collect all the market prices. However for a brand new product, there is not any market price and we have to look around similar products as well as the satisfactory price of customers about the new product, and create a well-defined pricing reference sub-model within the auxiliary data model. However, product pricing is very much dictated by the manufacturing costs as well, and they need to be worked out first too. Hence, cost features are useful for cost engineering throughout a product's life cycle. To do that, different levels of information from different angles are needed; hence, it is necessary to define product cost feature from deterministic relations among all the related elements from raw material costs to delivery costs of the product sales.
On the other hands, the proposed DM approach is based on another kind of data, which is intangible data, which means the data has no clear (or too complicated) relations with the targeted cost item. This kind of data has indirect effect on the cost estimation, such as the computer software licences cost that used in design and manufacturing. It is reasonable to assume that, after gathering all kinds of data with the help of modern enterprise software tools, like ERP systems, CADCAM tools, or process planning tools, the related cost feature member attributes and entities could be discovered by data mining algorithms. Relating cost features with the relevant data set selected among the huge amount of data is a challenging task that needs expertise.
5. Data Obtained by Each Employed Model
As shown in Fig. 1, the auxiliary data model contains ERP data, historical order data with cost components, and product model configuration data. Obviously, useful data has to be extracted from such information repositories for cost estimation purpose. Clearly, the design model can be cycled and the detailed design features searched and their pointers collected in a set because the design features have been implemented in the CADCAM data model when the products were developed according to design feature templates. Further, the output of searching machining process model can present the predefined process features. However, to extract cost data from the ERP and order data models to establish the cost feature objects, the cost feature templates have to be applied. To do so, the cost feature library has to be defined with the cost feature data structure and the data extraction methods required. It can be appreciated that the three data models contain only past order data and related design and manufacturing features, the related and explicit cost relations are not yet identified.
To solve cost feature identification problem, the historical order data with cost components from ERP data model has to be analysed and associated dynamically to the design and manufacturing features in order to justify the estimations and also directly support the functional estimation module. Therefore, the next step is to develop the feature mapping relations based on the results of the above data extraction procedure and identify those input relations that will be used as cost feature mapping technology.
Up to now, several methods was introduced for feature mapping, such as mathematical model [9]. To keep the implementation simple, the mapping matrix method suggested by Zhang et al. [10] is used for implementation in this work. The outcome of mapping matrix can illustrate the cost estimation function. By using the output function generated from the mapping matrix, the cost features are identified for each product cycle; and hence the accuracy of cost estimation will be increased.
6. Data Mining for Cost Feature Pattern Construction
Clustering and classifying the data can be useful for data management. The first step is clustering the available data according to application scopes. This step can be done in two ways: clustering and classifying according to the assembly principles of component analysis, or using clustering algorithm. Then, within each cluster, DM process can be used for further cost engineering. By applying DM in a cluster with the appropriate size, the accuracy of data mining results will be increased, because there is a set of common relations among the components with similar data patterns. Within the cluster, components will be classified by the same decision tree and rules.
The second step is to classify cost related data among components in a cluster. During the DM classification process, two kinds of data will be encountered: quantitative data and qualitative data. Quantitative data is a numeric data that needs to be classified by a decision tree via rule setting. Linear regression, K-nearest neighbour and baseline predictor are some common algorithms that can be used for analysing qualitative data.
In the next step, by analysing the combination of classified quantitative and qualitative data, the cost model patterns will be extracted. Model patterns can be used to filter the selected cost related data and as a result the cost feature constituents can be established with validated DM processes. At the end, these constituents, in the form of attributes or pattern data structures are clearly identified and created into reusable class elements. These elements are then further ranked according to the nature of the product that the cost estimation method will be applied. Also, there are several data mining algorithms reported for data ranking. Such as, best first, linear forward selection and ranker, which can be useful for data ranking. Then, one of the most effective ranking techniques can be selected based on the weight of data or accuracy of data [11]. Figure 3 shows the steps of auxiliary data modelling with more details. Table 3 shows two resulted patterns generated based on cost related data that can be used for the estimation of cost for producing door weldment. Note that the simple average cost per part accounting all the cost elements should be $831 for alternative 1 while $518 for alternative 2. However, the resulted average cost per part after data mining is not exactly the same. They are $787 and $483 respectively. The differences reflect the influence of intangible data on the final cost due to the inconsistent data sources and discretion by the management. The interpretation and accuracy evaluation for the data mining method are to be further studied in the future. The system design details are to be introduced in the next section.
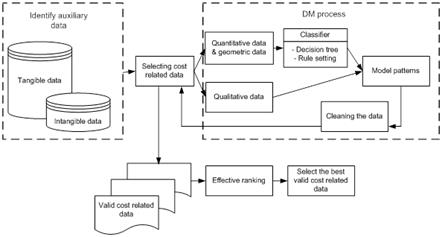
Table3. Generated output by integrated model.
|
Machine cost/yr ($) |
Licences cost/yr ($) |
Maintenance cost/yr ($) |
Labour cost/yr ($) |
Material cost per part ($) |
Output part/yr |
Average cost/part ($) |
Quality |
Alternative 1 |
420,620 |
25,000 |
420 |
1,600,000 |
45 |
2600 |
787 |
Good |
Alternative 2 |
320,000 |
25,000 |
360 |
1,200,460 |
35 |
3200 |
483 |
Fair |
7. System Design for Cost Estimation
As explained, having a unified cost estimation system is imperative for doing dynamic cost engineering throughout the stages of a product lifecycle.Figure 4 illustrates the computer system diagram for cost estimation which is designed with reference to the modules of an ERP system in use and the related product engineering models. Cost estimation system begins with the customer ordering process. The customer requirements are first collected, processed and recorded into the ERP customer relation management (CRM) module. Then such requirements are mapped into product functions which are defined by the product model series, and up into a customer specific product configuration. Based on such product concept model, the product unified feature model is established which includes design features, manufacture features and the corresponding cost features. Then, with the relevant information provided from the product model, the cost advisory system module needs to manage the cycles of "if-then" cycles about the costs. Via the cost advisory information UI of the system, the interactions between customer requirement and cost information, which are supported by the organized cost features, can be illustrated dynamically. From the synthesized cost results which are functionally supported by the cost advisory system, the customer is then informed on the estimated product cost much more accurately than using traditional rough estimates. After, cycles of evaluation on the cost vs. specifications of the product expected, the customer makes the purchasing decision and then a customer order is generated.
Once the customer order is confirmed, from here the cost management process kicks in. The cost management system is activated and the corresponding UI show the actual cost components of that customer order. In the next step, all the cost information from cost advisory system will be transferred to cost management module and it will also be used in the ERP system. Cost features are used in mapping cost related associations by referring design features and machining features under the product unified feature model.
8. Integration between Sub-models
Each of above models can be defined as a functional modular class: design class, machining class and auxiliary data class. Semantic data modelling between these three classes can provide the integrated system within different views on data; which can represent the structured and non-structured data [12]. To realize the expected functionality, several types of class relations among sub-models can be defined. A relation can be defined as a semantic link between two or more objects in the purpose of creating a logical system. Conceptually, a relation can be defined as an attributes, entity, independent element or function [13]. In general, the relation between classes can be defining as an aggregation, inheritance, using, association, and instantiation [14].
Figure 5 shows the UML diagram of integration between sub-models. Cost features are associated with all the three sub-models, or the three modular classes. First, there is an association relation between design feature class and machining feature class. Due to the interlocking nature of design and manufacturing considerations in real product lifecycles, there is some kind of mutual dependency link, cooperate, between these two classes. Auxiliary data model is an abstract modular class that has inheritance relationship from the design feature class and machining feature class. It means auxiliary data class is dependent on design feature class and machining feature class; and any change on the design and manufacturing will be automatically reflected on auxiliary data class properties. Cost features inherit data input from all the three sub-models; but the real relationship materialization can be constructed based on the input data and the data mining process results as discussed above. Therefore it is clear that cost features are modelled to take care of the intricate cost influencing relations initiated from design and machining features as well as other auxiliary data.
To clarify the interdependency relationship between design and machining features, more discussion is necessary. It can be appreciated that usually, the features that used for design have different definitions from machine features. Figure 6 shows a part of door weldment and their geometrical elements of design features and machine features on this part respectively. In design geometry, the part was defined by adding a small block on top of base block and cutting a curved notch from bottom of base block. On the other hand, the part machining process was defined by water jet cutting represented with machining feature profiles B, C and D.
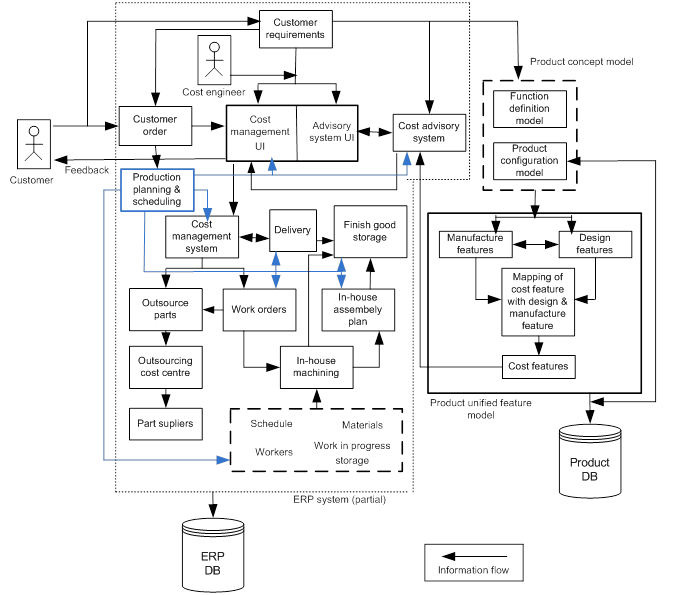
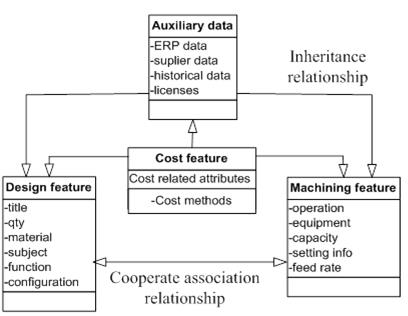
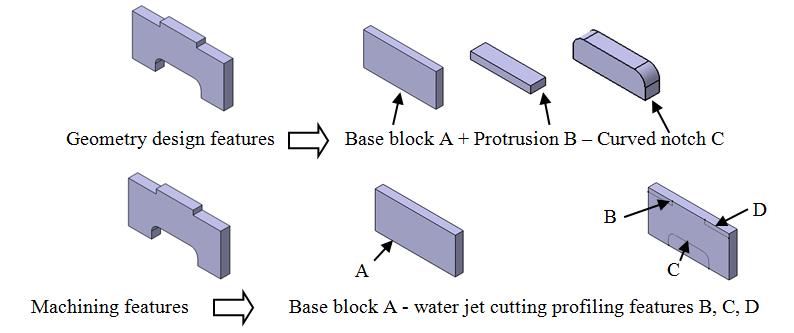
9. Conclusion
In this paper, the authors define a cost feature class, and then presented an overview of the relations between cost features and three engineering sub-models, i.e. machining model, design model and other auxiliary data model. For having the dynamic, unified and accurate cost estimation modelling, the relations among cost features and all engineering sub-models need to be managed consistently. The descriptive semantics of cost feature is flexible enough to represent all types of associations which are related to cost estimation, having deterministic and non-deterministic or fuzzy relations. For the latter type of relations, data mining is proposed as a useful method to extracting data patterns for these three sub-models. It was also discussed that clustering before data mining is helpful to assure the quality of the approach. Classifying cost feature elements according to data mining algorithms was proposed for intangible data analysis in the purpose of more accurate cost estimation. Currently, the data application and error evaluation have not been carried out yet. They are two important aspects to proof the proposed algorithm; and they will be addressed in the authors' future pulications.
Acknowledgements
The authors would like gratefully acknowledge the technical case study material was provided by McCoy Drilling and Completions (Farr) Company. The research work reflected in this paper was supported by a completed MITACS internship program, a NSERC discovery grant (355454-09) and a new NSERC CRD grant sponsored by McCoy. This research effort is carried out at University of Alberta, Edmonton, Canada.
References
[1] A. Niazi, J.S. Dai, S. Balabni, L. Seneviratne "Product Cost Estimation: Technique Classification and Methodology Review", Journal of Manufacturing Science and Engineering, 128(2), 2005, 563-575. View Article
[2] R. Bidarra, W.F. Bronsvoort "Semantic feature modelling" Computer-Aided Design, 32, 2000, 201–225. View Article
[3] Y.-S. Ma "Semantic Modeling and Interoperability in Product and Process Engineering", London, Springer, 2013. View eBook
[4] Y.-S. Ma, N. Sajadfar, L. Campos Triana "A feature-based semantic model for automatic product cost estimation" IACSIT International Journal of Engineering and Technology, 6(2), 2014, 109-113. View Article
[5] Y.-S. Ma, T. Tong "Associative feature modelling for concurrent engineering integration" Computers in Industry, 51, 2003, 51–71. View Article
[6] T. Lin, J-W. Lee, E.L.J. Bohez "New integrated model to estimate the manufacture cost and production system performance at the conceptual design stage of helicopter blade assembly" International Journal of Production Research, 50(24), 2012, 7210-7228. View Article
[7] K. Ulrich, S. Eppinger "Product Design and Development" Boston, MA: Irwin McGraw-Hill, 2000. View Book
[8] J.H. Han, M. Pratt, W. Regli "Manufacturing feature recognition from solid models: a status report" IEEE Transactions on Robotics and Automation, 16(6), 2000, 782-796. View Article
[9] Z. Liu, W. Bu, J. Tan "Motion navigation for arc welding robots based on feature mapping in a simulation environment" Robotics and Computer-Integrated Manufacturing, 26, 2010, 137–144 View Article
[10] D.L. Zhang, J. Qiao, J.B. Li, L.Y. Qiao, S.C. Chu, & J.F. Roddick "Optimizing Matrix Mapping with Data Dependent Kernel for Image Classification", Journal of Information Hiding and Multimedia Signal Processingm, 5(1), 2014. View Article
[11] A. Bernstein, F. Provost, S. Hill "Toward intelligent assistance for a data mining process: an ontology-based approach for cost-sensitive classification" IEEE Transactions on Knowledge and Data Engineering, 17(4), 2005, 503–518. View Article
[12] N.K. Shaw, M.S. Bloor, A. de Pennington "Product Data Models" Research in Engineering Design, 1(1), 1989, 43-50. View Article
[13] J. Peckham, F. Maryanski "Semantic Data Models" ACM Computing Surveys (CSUR), 20(3), 1988, 153-189. View Article
[14] J. Oliveira, P. Zave "FME 2001: Formal Methods for Increasing Software Productivity", Springer, 2001. View eBook